铜熔炼炉底用耐火捣打料的问题分析及改进-pg电子试玩平台
发布时间:2020/8/17 14:51:41
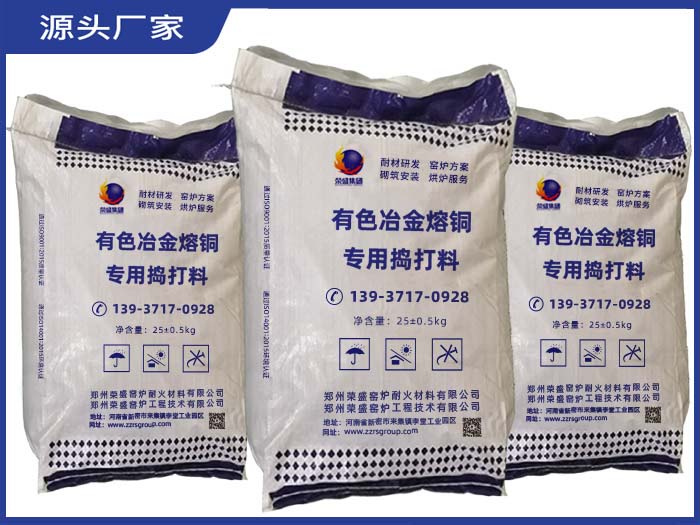
某中小型铜冶炼厂密闭鼓风炉、前床和连续吹炼炉炉底原设计采用石英砂为主的硅质耐火捣打料,,在使用过程中,发现其抗渗透损坏性能不佳,使炉底损蚀快,寿命短。针对其问题对炉子的炉底结构和使用的耐火捣打料性能进行分析。发现应用硅质捣打料出现了一系列的问题,故经过专家学者的一致研究,改用镁质耐火捣打料。
1、原设计炉底结构及耐火捣打料组成
1.1、密闭鼓风炉、原设计炉缸砌体结构如图1。与熔体接触的面层为镁铝砖,厚度230mm,错缝砌筑,下面为70mm厚捣打料,材料组成(重量比)为:3~5mm石英砂70%,生粘土粉30%,加模数295的水玻璃混合拌湿,人工砸实后用柴火烘干8h。
1.2、前床、原设计炉底砌体结构,与高温熔体接触的面层为镁铝砖,厚230mm,砌成反拱形。下层的捣打料厚34mm(反拱中线处),材料组成(重量比)为:3~8mm石英砂70%,生粘土粉30%,用水拌合均匀,掺水玻璃5%,砸实后烘干。
1.3、连续吹炼炉、原设计炉底砌体结构如图3,接触高温熔体的面层为镁铝砖,厚230mm,砌成反拱形。其下面的捣打料厚度140mm(反拱中心处),材料重量比组成与前床一致。
2、硅质捣打料存在问题剖析
通过仔细分析上述三炉底的结构和捣打料组成,不难发现如下情况和问题。
(1)三炉捣打料均处于面层镁铝砖的下面,与镁铝砖一道长期承受高温及熔体的巨大压力。捣打料层对面层镁铝砖是支承层,对下面和左右两侧砖体是保护隔离层。
(2)三炉捣打料组成原设计基本一致,均以石英砂为主构成水玻璃型硅质捣打料。石英砂是骨料,决定捣打料层理化指标的优劣:生粘土粉主要起填充剂作用,能减少空隙增加捣打层的致密性;水玻璃则起粘结胶合作用。
(3)三炉捣打料均为硅质,属酸性耐火材料;其面层为镁铝砖,材质为镁铝质,属碱性耐火材料,显然两者材质不一,属性相反。
(4)三炉炉底在熔炼过程中,要经受1200~1300℃的高温作用,硅质捣打层中的sio2与镁铝砖的mgo会起化学反应,生成橄榄石2mgo·sio2对镁铝砖产生损蚀作用。
(5)三炉熔炼过程中,所承载的高温熔体含有碱性成分cao、mgo、feo、cu2o等。当炉底面层镁铝砖因砖材质量、砌筑质量存在缺陷时,熔体便会向下透渗。当其碱性成分触及硅质酸性捣打料时,相互间就会产生化学作用,使捣打料受侵蚀,而产生疏松致穿等问题。
(6)以石英砂为主,添加生粘土粉及水玻璃组成的水玻璃型硅质捣打料,由于水玻璃粘结力不强,且没有添加促凝剂,捣打成型后整体性、致密性、结实度及烧结效果均不够理想。
(7)由于三炉捣打料属硅质,与镁质耐材相比,无论耐火度、耐压强度、体积密度、显气孔率、抗碱性氧化物性能等均存在较大差距。
3、耐火捣打料的改进
实践证明采用镁砂烧结或镁铁烧结炉底(用于与熔体直接接触)具有较大的机械强度、致密性好、坚韧性大和抗蚀性良好,炉底寿命显着延长。其做法是将镁砂(mgo>83%,粒度<5mm)、铁粉(fe3o473%、fe2o387%、feo17%)和卤水(mgcl2>45%)按比例配料混合后捣固,点火升温至1500℃,恒温38h后便形成完整的烧结炉底。本着捣打料材质选择与镁铝砖相近原则,决定将原设计的水玻璃硅质捣打料改为卤水加镁砂,并在密闭鼓风炉、前床和连续吹炼炉筑炉施工中同时采用。这种卤水加镁砂的镁质捣打料的重量比组成为:2~6mm镁砂67%,镁粉33%,氧化铁红适量,用卤水(d≥1.26)掺和拌合均匀后人工捣固,并用柴火烘干24h。材料要求为:镁砂,mgo≥80%,粒度2~4mm和4~6mm各50%配制而成;镁粉,牌号mf-82,粒度≤0.088mm;卤水用mgcl2≥45%的卤粉调配而成;氧化铁红,标准h103,一级品。施工中发现该镁质捣打料具有固结效果好,不经烘烤,自然养护也能较快地形成整体且致密性良好,强度增长快;施工工具方法简单,操作方便快捷。
耐火材料出现开裂、脱落、易磨损怎么办?想要彻底解决问题,需要从根源挖掘,分析出真正的原因,荣盛耐材从事耐材生产、研发服务多年,能解决高温窑炉内衬的各种疑难问题,欢迎广大新老朋友咨询及技术交流。
行业动态
- 循环流化床锅炉用到的耐火材料…
- 锅炉本体用刚玉耐磨浇注料,2.…
- 耐火浇注料和耐火可塑料哪个好…
- 窑炉保温用保温砖还是用保温浇…
- 回转窑应用及水泥窑用耐火材料…
- 窑炉内衬用耐火砖,还是用耐火…
- 65高铝耐火浇注料和65高铝砖性…
- 当荣盛耐材遇上chatgpt,这回答…
- 荣盛科技集团2023年品牌口号征…
- 耐火可塑料外加剂有哪些,开裂…
- 常见耐火材料原料、产品及窑炉…
- 怎么让耐火浇注料抗煤燃烧的气…
- 耐火浇注料有哪些优势,该怎么…
- 热烈欢迎新密市领导莅临荣盛科…
- 高铝耐火水泥特点及应用
- 闹元宵 | 换上新衣裳,来荣盛做…
- 喜讯!荣盛耐材被认定为「郑州…
- 特种耐火材料氮化硅结合碳化硅…
- 轻质保温浇注料的特点及性质介…
- 危废焚烧回转窑技术及内衬耐材…